Blog
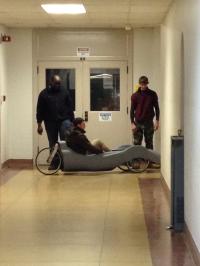
Our prototype car is coming back strong. After problems with the steering at competition last year, the team has come up with a new system and is in the process of testing it. All it needs now is a fresh coat of paint and it's ready to roll.
The new 50cc engine for the 2013 Eco-Car has arrived! The factory parts have been removed in preparation for our custom fuel injection system to be implemented. It will be at maximum fuel efficiency in no time.
The exterior shaping of the 2013 car has begun! Before any actual cutting can begin, the foam block must be aligned perfectly so that the outside cut lines up with the inside cut. To do this, holes were drilled through the block during the inside cut. When the block is flipped over, we find the the holes and line the drill up with them. It is quite a tedious process, but completely necessary. No one wants a lopsided car.
When you're trying to be as efficient as possible, it is very important to minimize the weight of the car. One way this is being practiced is by replacing old steel parts with lighter aluminum parts. The part being replaced here is a mount for an RPM sensor on the motor for HotRod. You may think the weight of something this small is negligible, but every ounce matters. Plus it looks better, too.
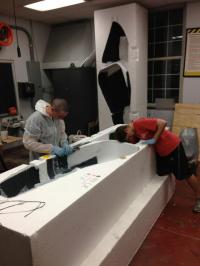
In order to stabilize our Styrofoam for the outer cut we lay carbon fiber inside over the crucial areas. You can see one half in the back already laid and the other half getting worked on. After this it gets the external cuts before we put the whole car together.